Refractory Maintenance Is Unavoidable, But An Experienced Crew With The Right Equipment Can Minimize Scheduled Downtime And Virtually Eliminate Installation Mistakes That Could Lead To Emergency Maintenance.
By Heather Harding

Time is money. No place is this adage more appropriate than the manufacturing industry. When even one piece of the system is down, whether for routine maintenance or an unexpected repair, lost production can cost facilities tens of thousands of dollars each day – that’s on top of any repair costs. Needless to say, minimizing maintenance downtime is key to overall efficiency and a healthy bottom line.
When it comes to cement kilns, the first step to achieve this is efficient, high-quality brick installation. Masons can extend kiln lining longevity and drastically reduce emergency maintenance by minimizing air gaps, interlocking rings or loose bricks.
To that end, masons are employing bricking machines in cement kilns across the globe to increase maintenance efficiency. Lightweight, heavy-duty machines can also provide fast ROI and extensive maintenance savings. Here’s how.
Time Savings
There is no avoiding the wait while a kiln cools. However, the productivity crews achieve once they are able to enter the kiln makes a significant difference on how long it takes to get things up and running again.
The time savings begins with the type of bricking machine and setup. A bricking machine constructed of strong, yet lightweight, modular aluminum components requires just one or two men to transport it into the kiln for assembly.
These bricking machine models can be installed in just 60 to 90 minutes with an experienced crew. Installation of other bricking machines made up of mostly steel components can take 6 to 8 hours, resulting in a full shift of lost revenue in set up alone.
Once installed, the bricking machine offers a mobile working platform capable of supporting as many as three pallets of bricks, depending on model, the personnel working on it and their tools. The arch is equipped with pneumatic cylinders, which are used to raise the bricks into place against the kiln shell. It is supported by a cart and a rail system to allow the arch to move along the length of the platform scaffold.
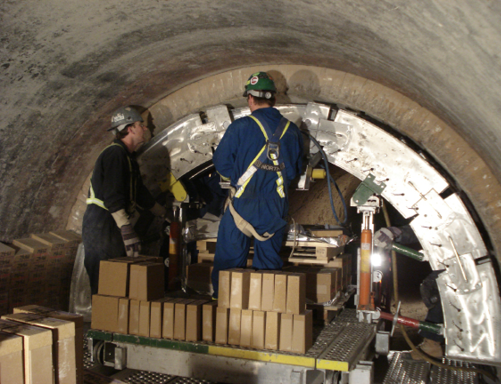
modular aluminum components require just one or two
men to transport it into the kiln for assembly.
Dual Arches Double Production
Not all bricking machines are created equal, though. As with any piece of equipment, quality matters. In addition to bricking machines created in-house, there are a number of models available from original equipment manufacturers. These feature a range of options that can have an impact on overall productivity.
The latest bricking machine technology incorporates double arches, permitting a second ring of brick to be installed while the first ring is being keyed. This accelerates installation over not only traditional installation methods, but earlier bricking machine models. Individual cylinder controls allow single-cylinder extension as needed, speeding up installation. And once the arch is complete, actuating the master valve lowers all the cylinders at once. There is no back and forth while installing bricks.
The difference in speed and efficiency between styles of bricking machines was proven to plant owners in Midlothian, Texas. Their previous refractory installation method was a Swedish Single Arch bricking machine that had an average of 73.4 hours of outages and downtime per year. After switching to a dual arch bricking machine, the plant’s downtime for maintenance decreased by 44%, resulting in a profit increase of $367,000 per year – providing a return on investment after one installation.
Likewise, a cement plant located in La Calera, Chile, had suffered numerous outages, unscheduled maintenance, damaged equipment and lost refractory. Analysts determined a number of factors were leading to the lost revenue, including mechanical defects of the kiln and inadequate brick installation quality using their Swedish bolt and timber machine.
The contractor was no longer used. Instead, plant personnel trained staff to replace the refractory brick using a bricking machine. That staff, which works with refractory bricking no more than twice a year, is now able to reline more than 46 ft. (14 meters) per shift.
This results in a total time of less than a week for heavy coating brick removal and relining of 98 ft. (30 meters) – cooling and heating included. However, installation time is only one small component and speed is nothing without quality.
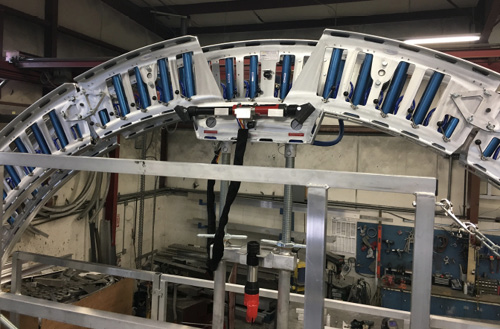
arches, permitting a second ring of brick to be installed
while the first ring is being keyed.
Installation Quality
With refractory issues like spiraling and twisting accounting for as much as 50% of unscheduled outages, ensuring a tight and good-quality fit is key to preventing failures.
Refractory installation methods that require installers to rotate the kiln make it difficult to maintain radial alignment of the brickwork, a critical factor for a stable brick lining. Improperly aligned brickwork cannot uniformly absorb the pressure from vertical refractory and could prematurely fail.
Rotating the kiln also leaves a large amount of unkeyed brick positioned straight up while the keying section is at the kiln’s waistline. Even if the keying is perfect, gravity will cause the unkeyed brickwork to sag, increasing the potential for catastrophic brick ring collapse.
This is not only time intensive and costly to rectify, it’s also a major safety concern. In addition, these installation methods run a high risk of rings interlocking with adjacent rings – potentially resulting in a domino effect of failing brick rings – and air gaps left between the brickwork and shell.
The La Calera plant saw the cost of quality issues quickly spinning out of control. Experiencing emergency shutdowns at least every three months, plant management reached a breaking point when bricks started falling out just two weeks after a repair. Poor quality installation was determined to be a major catalyst for the unscheduled shutdowns.
Poorly installed bricks led to interlocking rings and severe air gaps in the kiln lining. To compound matters, the added pressure of a kiln tire, which placed mechanical stress on the brickwork, contributed to the quick and costly failure. The failure led to an emergency shutdown resulting in more than $360,000 in lost revenue.
A modern bricking machine’s arches help to ensure quality control by holding each brick firmly against the kiln shell until the key brick is installed, ensuring a tight fit and virtually eliminating the risk of sagging. A hydraulic jack holds the unkeyed ring when moving the machine’s arch system.
This provides ample outward pressure for tight keying. Pneumatic cylinders are not released until the keying is complete, ensuring proper compressive forces. The master valve retracts or extends all cylinders simultaneously, allowing the arch to advance to the next row. The resulting high quality of installation can extend the life of the kiln lining by as much as 25%.
Unique design features, such as cut-away sections, further increase efficiency and productivity. The cut-away section in the front arch provides both ease-of-installation and visibility. It allows key masons an unobstructed area to place the key bricks.
Alternate bricking machine designs don’t include an opening in the arch, requiring installers to try to find ways to reach around the arch, reducing speed of installation and – potentially – quality. The cut-away section also allows key masons to see the previously keyed ring and use it as a guideline, enabling discovery of bricking errors sooner when all pneumatic cylinders are released to check for sagging.
By changing methods to achieve higher quality installations, the plant in La Calera was able to decrease the number of outages experienced by 75% to an average of three days per year. Even better, they eliminated costly unscheduled repairs, which were once their only stoppages, and now address maintenance on their own schedule when manpower, materials and equipment are ready.
Prior to using a bricking machine, the plant never went more than 90 days without refractory failure. Now the plant runs as long as 18-months before an outage. In fact, required scheduled maintenance was cut by 66%.
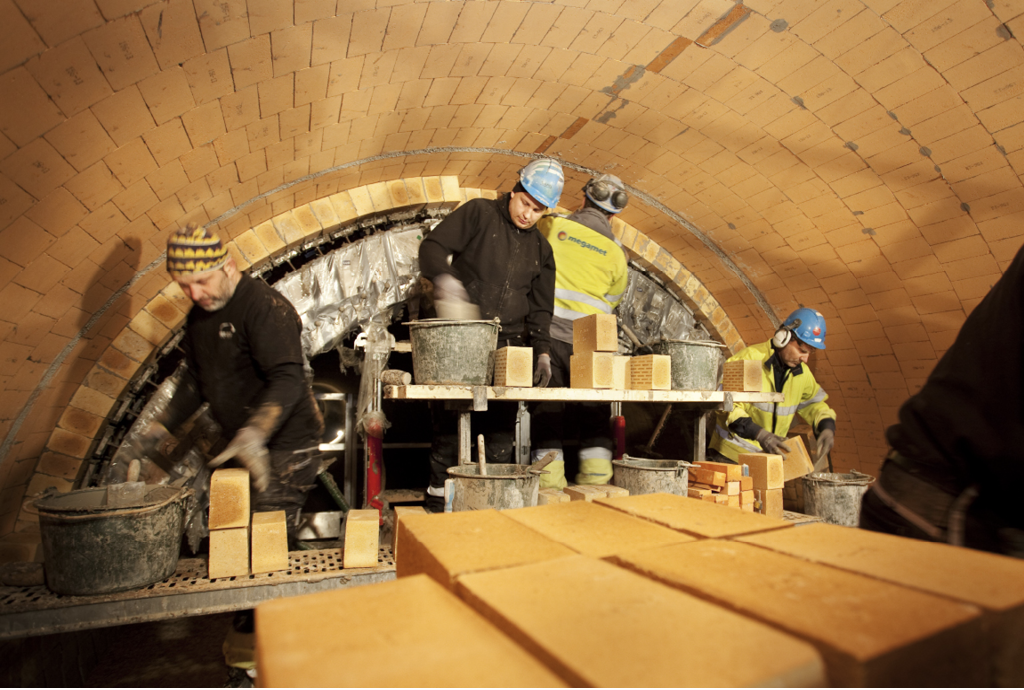
Coming Full Circle
High-quality installation has a positive impact on the longevity and performance of refractory lining. And increased productivity means maintenance is completed faster, as well. These advantages can end up saving an operation hundreds of thousands of dollars.
Refractory maintenance is unavoidable, but an experienced crew with the right equipment can minimize scheduled downtime and virtually eliminate installation mistakes that could lead to emergency maintenance. Offering faster installation and improved brickwork quality, a bricking machine provides long-term savings on kiln maintenance applications.
Heather Harding is the managing director for Bricking Solutions, a provider of kiln refractory installation solutions.